Solder Mask
Removable Mask for Wave Soldering, Conformal Coating & More
Chemask Solder Mask protect PC boards, plated thru-holes, contacts, pins, posts, terminals and gold fingers during wave soldering. They provide short-term high-temperature protection from molten solder to 515ºF/268ºC. All solder masks are nonflammable, non-contaminating and will not leave
Chemask WF can be removed in a batch or inline cleaning system, and will not clog filters or damage ion filter beds. Peelable solder masks are commonly used in no-clean soldering environments or by PCB assemblers that clean with solvents. Peelable masks are commonly used for masking contact areas and over chemically sensitive components in conformal coating processes.
Removal Method
Dispensing Methods
Sensitive Metal
Environmental & Safety
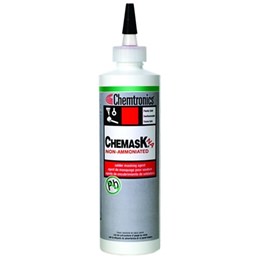
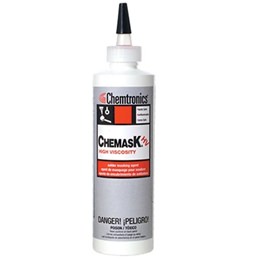
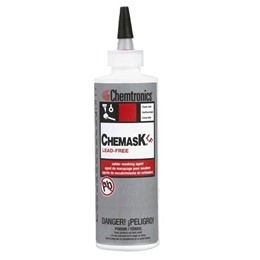
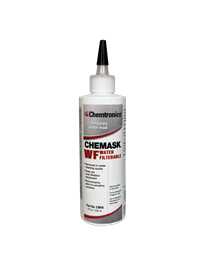