Wipes
Highest Quality Poly Cellulose, Polyester & Nylon Wipes for Cleanroom & More
Coventry™ cleanroom wipes keep contamination out of your process, improve yield, and perform consistently, shipment to shipment. To manufacture a Coventry swab, we start with engineered clean materials. Polyester materials are laundered first in our Class 10 (ISO Class 4) cleanroom.
Chemtronics dry wipes are engineered for controlled environments, light industrial, benchtop, and laboratory applications. They feature high absorbency, low contamination, high-purity, and little or no linting.
Application
Attributes
Cleanroom
Material
Environmental & Safety
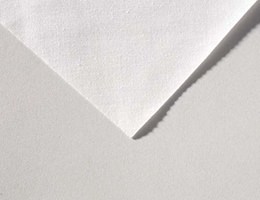
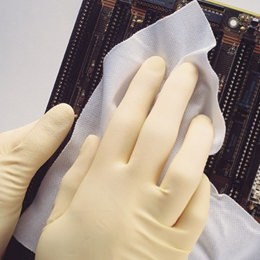